Highlighted Projects:
Devore, CA - 380’ of 48” casing / 100% hand mined
California Auger Boring performed a crossing 100% hand mined in Devore, California for Delta Pipeline. The crossing consisted of installing approximately 380’ of 48” casing used as a vessel for an 8” carrier pipe. The soil conditions encountered were nothing less than brutal. This crossing was executed successfully utilizing a Subsurface MMTS Handmining/JackingSled in combination with a specially trained hand mining crew and experienced trenchless consulting. Cobbles up to 40” in diameter, naturally cemented to the surrounding soil, were hand excavated and removed , one by one, through the casing. Inching the 48” casing thru at 1’ increments to the exit point at an astonishing 0.01” lower than target depth and line! These conditions would have typically rendered such a crossing as unboreable and then abandoned with conventional boring methods.
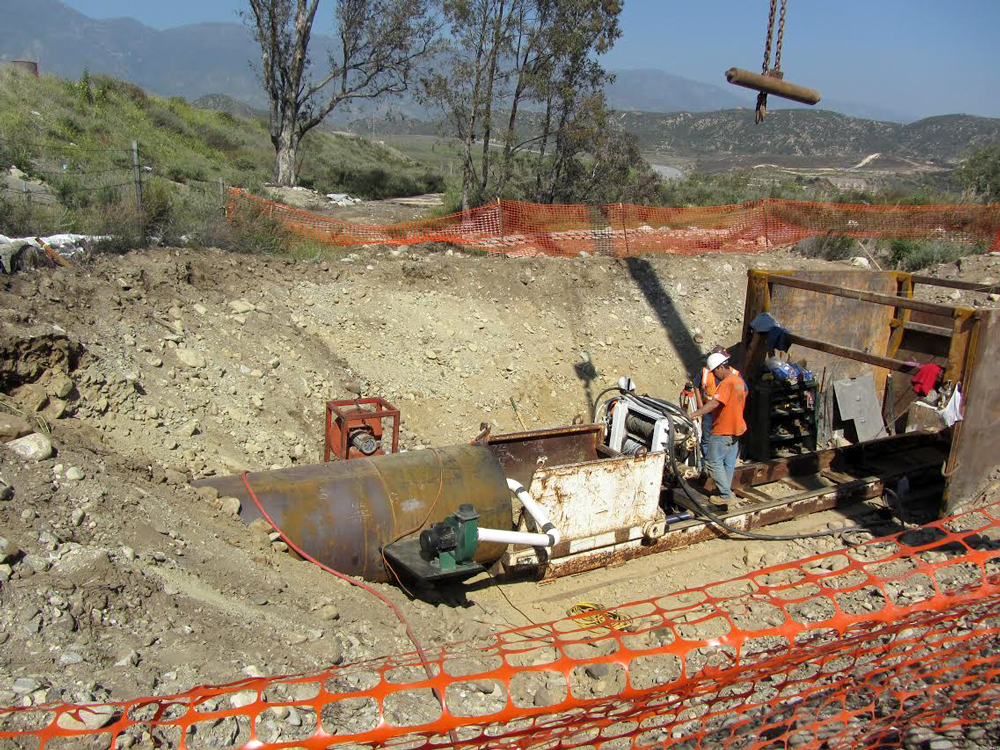
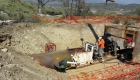
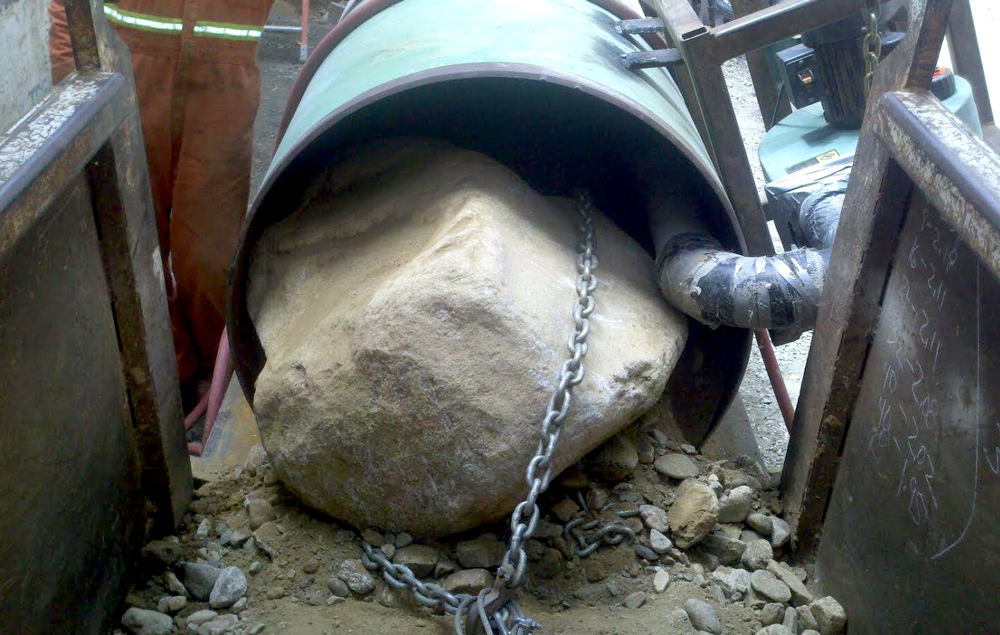
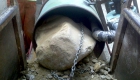
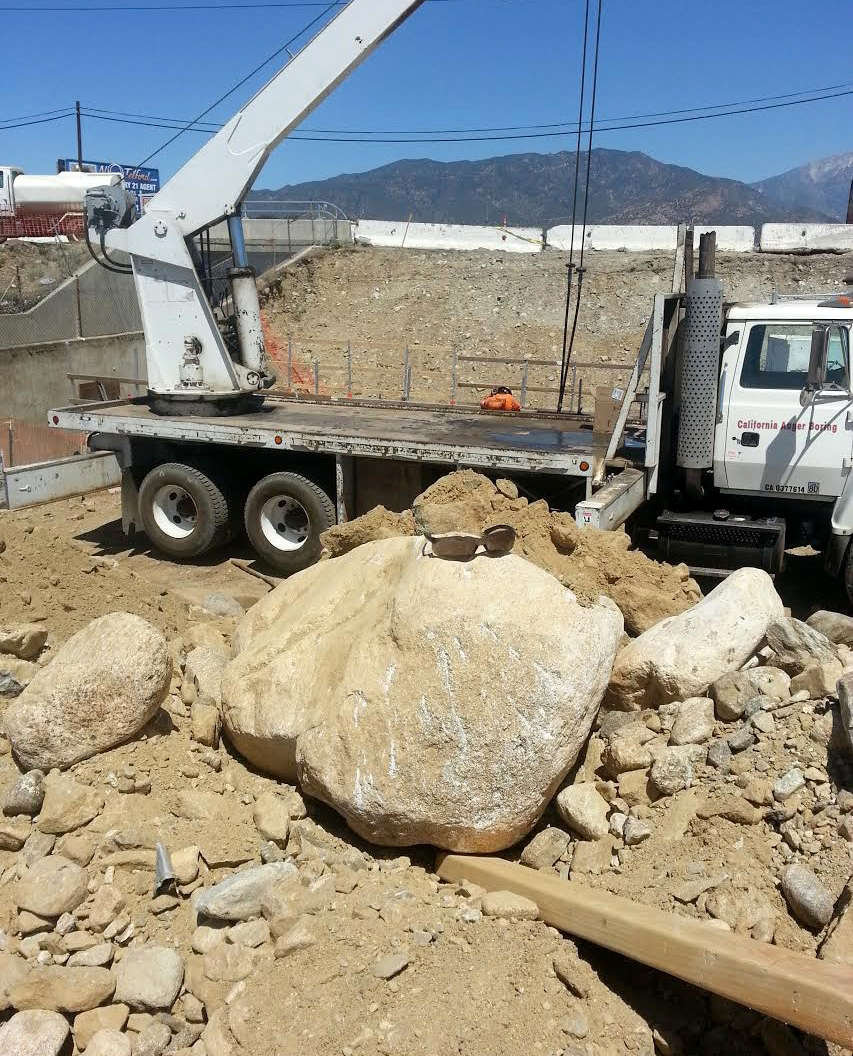
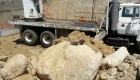
Long Beach, CA - (3) 24” casings side by side / 1 Week
California Auger Boring was called on to bore (3) 24” casings side by side, for OXY at the Port of Long Beach as contracted through ARB . The entire project had a tight, non-negotiable deadline which CAB committed the resources to work the project 24 hours around the clock . The bore elevations were such that CAB was required to set up above ground with a custom built concrete thrust backstop to brace the jacking rigs anticipated thrust loading. CAB was able to stitch each casing through the critical bore path, boring between concrete pilings utilizing an American Augers 36-600 bore rig in conjunction with an MMTS Steering Head for line and grade maintenance. Total project time from set up to tear down was an unparalleled 1 week.
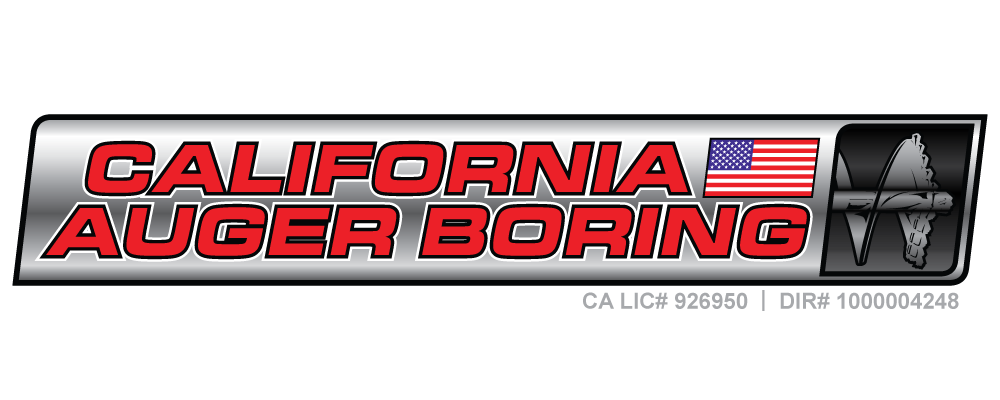
Thermal, CA - 704’ of 42” casing
In the hot desert region of Thermal, CA, California Auger Boring tackled a critical path bore of 42” casing approximately 704’ in length. CAB mobilized a American Augers 60-1200 to power through the subsurface and a 42” MMTS Steering head to navigate across the section of highway to a remote exit pit. An expansive , sticky clay was encountered mid bore at which point a bentonite injection system was run on the inside of the casing to coat the augers so the clay would not stick to the augers and could be conveyed back to the jacking pit. Faced with severe ground water and pit dewatering issues, the highly trained bore crew was able to traverse the entire length of the bore completing it at within 0.05” of the vertical and horizontal target destination.
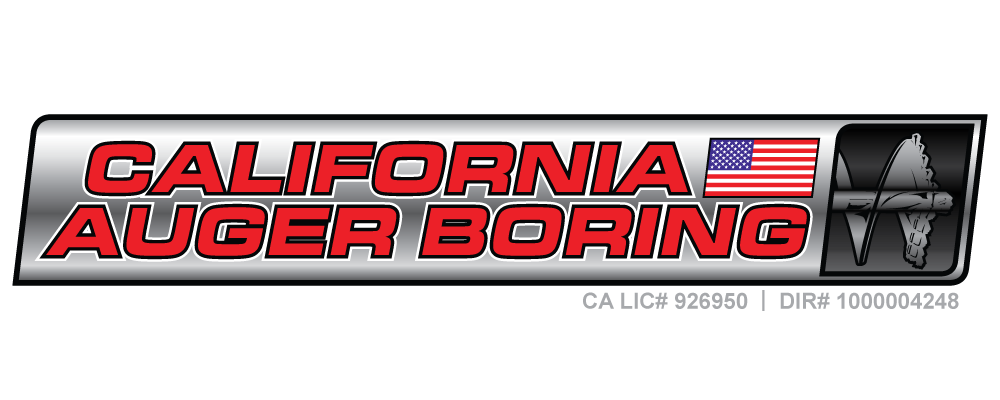
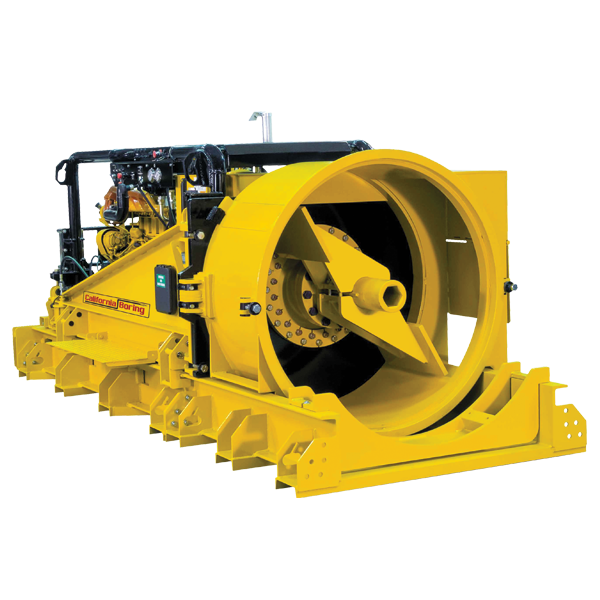